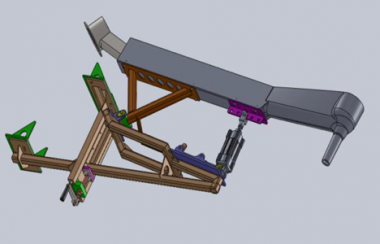
Introduction
KROWN S.A. is a company dedicated to the manufacture of industrial furnaces for the aluminium industry and is a pioneer in the pressure foundry. Their constant technological advances are based in the upgrade of the products developed by aluminium foundries, offering solutions to real problems that can happen every day with new technologies applied directly to the melting and dosing furnaces.
The industry in general, and especially the automotive sector, are demanding high quality structural parts with thin walls and high mechanical properties.
TECHNOLOGY CONTRIBUTION BY KROWN, S.A
The advantages that the KROWNMATIC dosing furnace offers against the traditional automatic loaders are well known and very important to keep in mind in the manufacture of high quality castings.
Some of these are:
- Dosing accuracy of +/- 1%
- 1/3 of less electrical consumption
- Aluminium loses by oxidation less than 0.05%
- Aluminium with less oxide
- Higher control and therefore more security of the process
However, it is an important metallurgical development to produce a clean and gas free aluminium. The new solution that KROWN offers is the elimination of the launder, and introducing in the market the UP-DOWN® System. This new system consists of introducing the liquid metal from the bottom of the shoot sleeve towards the top due to the pneumatic elevation of the launder that will permit the injection without turbulence (picture 1).

picture 1 UP-DOWN® system workout
- The main advantages of this new system are:
- Appropriate system especially for thin walled castings
- Porosity reduced to the minimum
- Castings with the possibility of heat treatment
- Welding castings
- High mechanical properties
KROWNMATIC Metal Quality
Aluminium castings must be virtually free of hydrogen porosity and entrained non-metallic inclusions. Negligence in reducing the dissolved hydrogen content of the melt, mitigating the formation of inclusions or removal of impurities, can result in premature failure of castings, broken machine tools or poor mechanical properties.
UP-DOWN® system
There are different metal qualities depending on the dosing launders used. Apart from other sources, gas porosity occurs from entrapped air and forms AI²0ᵌ at the surface exposed to the atmosphere during mould filling. The more turbulent the filling process the higher is the concentration of gas and non-metallic inclusions because the surface exposed to the atmosphere is greater.
The degradation of mechanical properties mainly depends on the size and distribution of the oxide inclusions and porosity. The goal of designing a launder UP-DOWN® is to maintain the flow and the mould filling in a non-turbulent way to minimise the gas content (
Normal launders can induce proportions of non-metallic inclusions ˃1mm²/kg in certain segregation zones measured and gas porosity ˃0.1 ml/100g.
The data taken when the launder UP-DOWN® is installed show aluminium oxides below 0.07 mm²/kg and gas porosity below 0.1 ml/100g after degassing, filtering and fluxing in ladles. These values permit the alloys used in the foundry to manufacture premium engineered castings providing higher levels of quality and reliability than are found in conventional produced parts and displaying optimum performance in mechanical properties, soundness, dimensional accuracy and finish.
The high performance allows our customers to produce parts with structural integrity even in thin walls.
Conclusions
The use of a special launder design UP-DOWN® enables foundries to produce castings with aluminium oxide inclusions clearly below the critical values 0.2 - 0.3 mm²/kg. The data taken over the melts degassed, filtered and fluxed are
The gas porosity is maintained below 0.1 ml/100g. This porosity level and the aluminium oxide inclusions, permits the foundry to produce premium engineered casting products with a furnace KROWNMATIC.
By Martinez Alcolea, A.y Vicente Martinez, M.A.